La începutul lunii august 2016, marina SUA a testat cu succes tiltrotorul Osprey MV-22. Acest avion în sine nu este neobișnuit. Vehiculul cu două rotori a fost în funcțiune cu marina americană de mult timp (a fost dat în exploatare în a doua jumătate a anilor 1980), dar pentru prima dată în istorie, piese critice au fost instalate pe un tiltrotor (siguranța zborului depinde direct de ele), care au fost imprimante 3D.
Pentru testare, armata SUA a tipărit o consolă pentru atașarea motorului la aripa tiltrotorului din titan folosind sinterizarea laseră strat-cu-strat direct. În același timp, un suport de măsurare a fost montat pe suport, conceput pentru a înregistra o posibilă deformare a piesei. Fiecare dintre cele două motoare ale oscilatorului Osprey MV-22 este atașat la aripă folosind patru astfel de consolă. În același timp, în momentul primului zbor de test al tiltrotorului, care a avut loc la 1 august 2016, pe acesta a fost instalat un singur suport, tipărit pe o imprimantă 3D. Mai devreme s-a raportat că suporturile de nacelă tipărite prin metoda de imprimare tridimensională au fost instalate și pe tiltrotor.
Dezvoltarea pieselor tipărite pentru tiltrotor a fost realizată de Centrul de operațiuni de luptă a aviației US Navy situat la baza comună McGuire-Dix-Lakehurst din New Jersey. Testele de zbor ale Osprey MV-22 cu piese tipărite au fost efectuate la baza râului Patxent al Marinei SUA, testele au fost recunoscute de militari ca fiind complet reușite. Armata americană consideră că, datorită introducerii pe scară largă a tipăririi tridimensionale, tehnologia în viitor va putea produce rapid și relativ ieftin piese de schimb pentru convertoare. În acest caz, detaliile necesare pot fi tipărite direct pe nave. În plus, piesele tipărite pot fi apoi modificate pentru a îmbunătăți performanțele ansamblurilor și sistemelor de la bord.
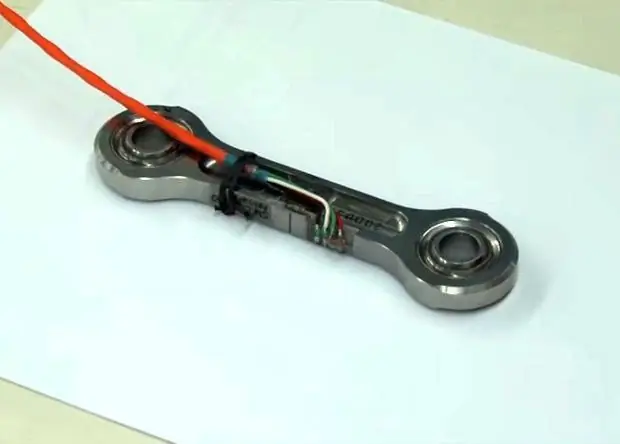
Suport de montare a motorului imprimat cu titan
Armata SUA era interesată de tehnologiile de imprimare 3D în urmă cu câțiva ani, dar până de curând, funcționalitatea imprimantelor 3D nu era suficient de largă pentru a putea fi utilizată în mod obișnuit pentru a construi piese destul de complexe. Piesele pentru tiltrotor au fost create folosind o imprimantă 3D aditivă. Piesa este realizată treptat în straturi. La fiecare trei straturi de praf de titan sunt legate cu un laser, acest proces se repetă atât timp cât este necesar pentru a obține forma dorită. După finalizare, excesul este tăiat din piesă; elementul rezultat este complet gata de utilizare. Întrucât testele au fost finalizate cu succes, armata americană nu se va opri aici, urmând să construiască încă 6 elemente structurale importante ale tiltrotorului, jumătate dintre acestea fiind tot titan, iar cealaltă - oțel.
Imprimarea 3D în Rusia și în întreaga lume
În ciuda faptului că tipul de producție al imprimantei a fost implementat cu succes în SUA și Rusia în urmă cu câțiva ani, crearea de elemente pentru echipamentul militar este în curs de finalizare și testare. În primul rând, acest lucru se datorează cerințelor foarte ridicate pentru toate produsele militare, în principal în ceea ce privește fiabilitatea și durabilitatea. Cu toate acestea, americanii nu sunt singuri care fac progrese în acest domeniu. Pentru al doilea an consecutiv, designerii ruși au produs piese pentru puști de asalt și pistoale dezvoltate folosind tehnologia de imprimare 3D. Noile tehnologii economisesc timp valoros de desen. Iar punerea în funcțiune a acestor piese poate asigura înlocuirea rapidă pe teren, în batalioane de reparații, deoarece nu va mai fi nevoie să așteptați piese de schimb din fabrică pentru aceleași tancuri sau vehicule aeriene fără pilot.
Pentru submarinisti, imprimantele 3D militare vor merita pur si simplu greutatea lor in aur, deoarece in cazul navigatiei autonome pe distante lungi, inlocuirea pieselor de catre submarinisti insisi va da submarinului o resursa aproape inepuizabila. O situație similară se observă cu navele care fac călătorii lungi și spargătoare de gheață. Majoritatea acestor nave vor primi drone în viitorul foarte apropiat, ceea ce va necesita în cele din urmă repararea sau înlocuirea completă. Dacă pe navă apare o imprimantă 3D, care va face posibilă imprimarea rapidă a pieselor de schimb, atunci în câteva ore echipamentul poate fi folosit din nou. În condițiile tranzitoriei operațiunilor și a mobilității ridicate a teatrului de operațiuni militare, asamblarea locală a anumitor părți, ansambluri și mecanisme chiar la fața locului va permite menținerea unui nivel ridicat de eficiență a unităților de sprijin.
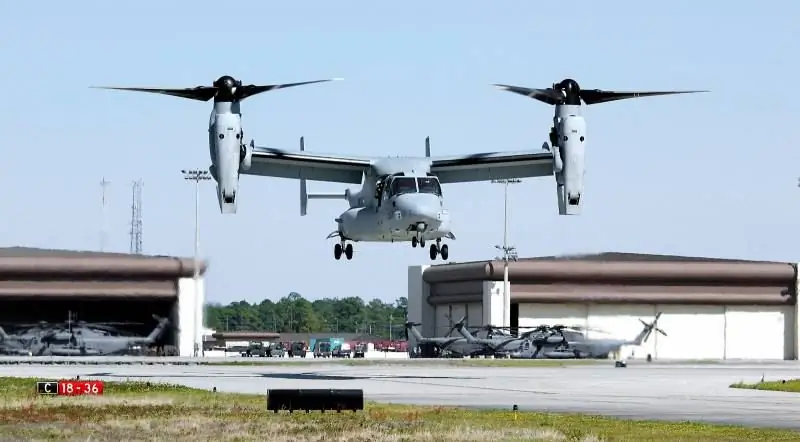
Osprey MV-22
În timp ce armata SUA își lansează convertiplanele, producătorii ruși ai tancului Armata folosesc deja o imprimantă industrială la Uralvagonzavod pentru al doilea an. Cu ajutorul său, sunt produse piese pentru vehicule blindate, precum și produse civile. Dar până acum, astfel de piese sunt folosite doar pentru prototipuri, de exemplu, au fost utilizate la crearea tancului Armata și a testelor sale. La Preocuparea Kalashnikov, precum și la TsNIITOCHMASH, din ordinul armatei ruse, designerii realizează diverse părți ale armelor mici din cipuri metalice și polimerice folosind imprimante 3D. Biroul de proiectare a instrumentelor Tula, numit după Shipunov, faimosul CPB, cunoscut pentru un sortiment bogat de arme fabricate: de la pistoale la rachete de înaltă precizie, nu rămâne în urmă. De exemplu, un pistol promițător și o pușcă de asalt ADS, care sunt destinate să înlocuiască forțele speciale AK74M și APS, sunt asamblate din piese din plastic de înaltă rezistență care sunt imprimate pe o imprimantă. Pentru unele produse militare, CPB a reușit deja să creeze matrițe; în prezent, se lucrează la asamblarea în serie a produselor.
În condițiile în care se observă o nouă cursă a înarmărilor în lume, momentul eliberării de noi tipuri de arme devine important. De exemplu, în vehiculele blindate, doar procesul de creare a unui model și transferul acestuia de la desene la un prototip durează de obicei un an sau doi. La dezvoltarea submarinelor, această perioadă este deja de 2 ori mai lungă. „Tehnologia de imprimare 3D va reduce perioada de timp de câteva ori la câteva luni”, notează Alexey Kondratyev, expert în domeniul marinei. - Proiectanții vor putea economisi timp pe desene atunci când proiectează un model 3D pe computer și pot realiza imediat un prototip al piesei dorite. Foarte des, piesele sunt reprelucrate ținând cont de testele efectuate și în curs de revizuire. În acest caz, puteți elibera ansamblul în locul piesei și puteți verifica toate caracteristicile mecanice, modul în care părțile interacționează între ele. În cele din urmă, momentul prototipării va permite proiectanților să reducă timpul total pentru ca primul eșantion finalizat să intre în etapa de testare. În zilele noastre, este nevoie de aproximativ 15-20 de ani pentru a crea un submarin nuclear de nouă generație: de la o schiță la ultimul șurub în timpul asamblării. Odată cu dezvoltarea în continuare a tipăririi tridimensionale industriale și lansarea producției în serie de piese în acest mod, intervalul de timp poate fi redus de cel puțin 1,5-2 ori."
Potrivit experților, tehnologiile moderne sunt acum la unul sau doi ani distanță de producția în masă de piese din titan pe imprimante 3D. Este sigur să spunem că până la sfârșitul anului 2020, reprezentanții militari la întreprinderile complexului militar-industrial vor accepta echipamente care vor fi asamblate cu 30-50% folosind tehnologii de imprimare 3D. În același timp, cea mai mare importanță pentru oamenii de știință este crearea de piese ceramice pe o imprimantă 3D, care se disting prin rezistență ridicată, ușurință și proprietăți de protecție termică. Acest material este utilizat pe scară largă în industria spațială și aeriană, dar poate fi utilizat în volume și mai mari. De exemplu, crearea unui motor ceramic pe o imprimantă 3D deschide orizontul pentru crearea de aeronave hipersonice. Cu un astfel de motor, un avion de pasageri ar putea zbura de la Vladivostok la Berlin în câteva ore.
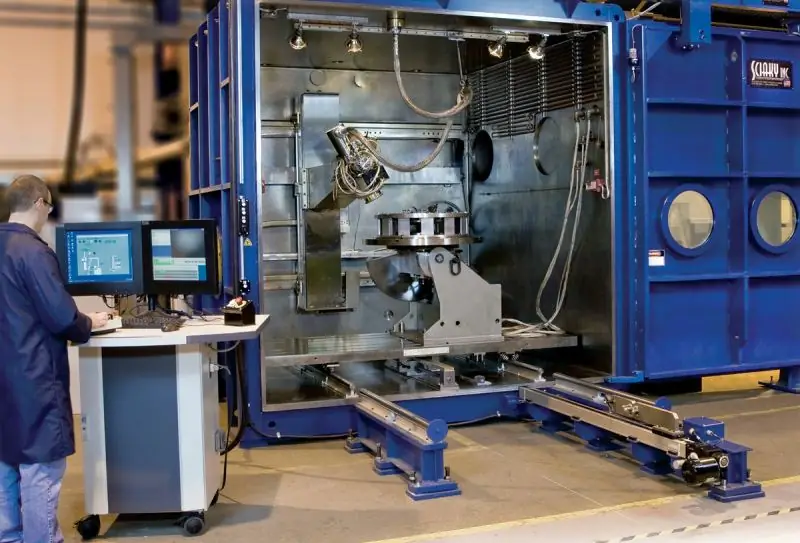
De asemenea, este raportat că oamenii de știință americani au inventat o formulă de rășină specială pentru imprimarea în imprimante 3D. Valoarea acestei formule constă în rezistența ridicată a materialelor obținute din aceasta. De exemplu, un astfel de material poate rezista la temperaturi critice care depășesc 1700 de grade Celsius, care este de zece ori mai mare decât rezistența multor materiale moderne. Stephanie Tompkins, directorul științei pentru cercetarea avansată în domeniul apărării, estimează că noile materiale create cu imprimante 3D vor avea combinații unice de caracteristici și proprietăți nemaivăzute până acum. Datorită noii tehnologii, Tompkins spune că vom putea produce o piesă durabilă, ușoară și uriașă. Oamenii de știință cred că producția de piese ceramice pe o imprimantă 3D va însemna o descoperire științifică, inclusiv în producția de produse civile.
Primul satelit rus 3D
În prezent, tehnologia de imprimare 3D produce deja piese direct la bordul stațiilor spațiale. Dar experții interni au decis să meargă și mai departe, au decis imediat să creeze un microsatelit folosind o imprimantă 3D. Rocket and Space Corporation Energia a creat un satelit, corpul, consola și o serie de alte părți din care au fost imprimate 3D. În același timp, o clarificare importantă este că microsatelitul a fost creat de inginerii Energia împreună cu studenții Universității Politehnice Tomsk (TPU). Primul satelit imprimantă a primit numele complet „Tomsk-TPU-120” (numărul 120 din nume în cinstea a 120 de ani de la universitate, care a fost sărbătorită în mai 2016). A fost lansat cu succes în spațiu în primăvara anului 2016 împreună cu nava spațială Progress MS-02, satelitul a fost livrat către ISS și apoi lansat în spațiu. Această unitate este primul și singurul satelit 3D din lume.
Satelitul creat de studenții TPU aparține clasei de nanosateliți (CubSat). Are următoarele dimensiuni 300x100x100 mm. Acest satelit a fost prima navă spațială din lume care a avut un corp imprimat 3D. În viitor, această tehnologie ar putea deveni o adevărată descoperire în crearea sateliților mici, precum și să facă utilizarea lor mai accesibilă și mai răspândită. Proiectarea navei spațiale a fost dezvoltată la Centrul științific și educațional TPU „Tehnologii moderne de producție”. Materialele din care a fost fabricat satelitul au fost create de oamenii de știință de la Universitatea Politehnică din Tomsk și Institutul de fizică a forței și știința materialelor din filiala siberiană a Academiei de Științe din Rusia. Scopul principal al satelitului a fost testarea noilor tehnologii de știință a materialelor spațiale; va ajuta oamenii de știință ruși să testeze mai multe evoluții ale universității Tomsk și ale partenerilor săi.
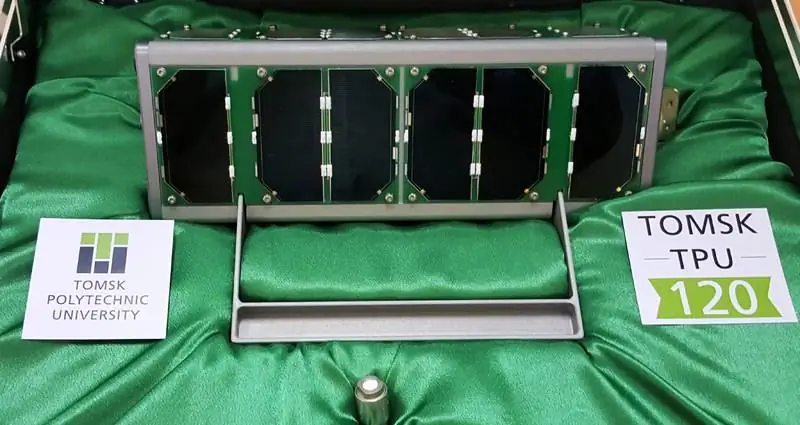
Potrivit serviciului de presă al universității, lansarea nanosatelitului Tomsk-TPU-120 a fost planificată să fie efectuată în timpul mersului spațial de la ISS. Satelitul este o navă spațială destul de compactă, dar în același timp, echipată cu baterii, panouri solare, echipamente radio la bord și alte dispozitive. Dar principala sa caracteristică a fost că corpul său a fost imprimat 3D.
Diferiti senzori ai nanosatelitului vor inregistra temperatura la bord, pe baterii si placi, precum si parametrii componentelor electronice. Toate aceste informații vor fi apoi transmise pe Pământ online. Pe baza acestor informații, oamenii de știință ruși vor putea analiza starea materialelor din satelit și vor decide dacă le vor folosi în dezvoltarea și construcția de nave spațiale în viitor. Trebuie remarcat faptul că un aspect important al dezvoltării navelor spațiale mici este, de asemenea, formarea de personal nou pentru industrie. Astăzi, studenții și profesorii Universității Politehnice din Tomsk, cu propriile mâini, dezvoltă, fabrică și îmbunătățesc proiectele tuturor tipurilor de nave spațiale mici, obținând în același timp nu numai cunoștințe fundamentale de înaltă calitate, ci și abilitățile practice necesare. Acesta este ceea ce face absolvenții acestei instituții de învățământ specialiști unici în viitor.
Planurile viitoare ale oamenilor de știință ruși și ale reprezentanților industriei includ crearea unui roi de sateliți universitari. „Astăzi vorbim despre necesitatea motivării studenților noștri să studieze tot ceea ce, într-un fel sau altul, este legat de spațiu - poate fi energie, materiale și crearea de motoare de nouă generație etc. Am discutat mai devreme că interesul pentru spațiu din țară s-a estompat oarecum, dar poate fi reînviat. Pentru a face acest lucru, este necesar să porniți nici măcar de la banca unui elev, ci de la una școlară. Astfel, ne-am angajat pe calea dezvoltării și producției CubeSat - sateliți mici”, - notează serviciul de presă al Institutului Politehnic Tomsk cu referire la rectorul acestei instituții de învățământ superior, Peter Chubik.