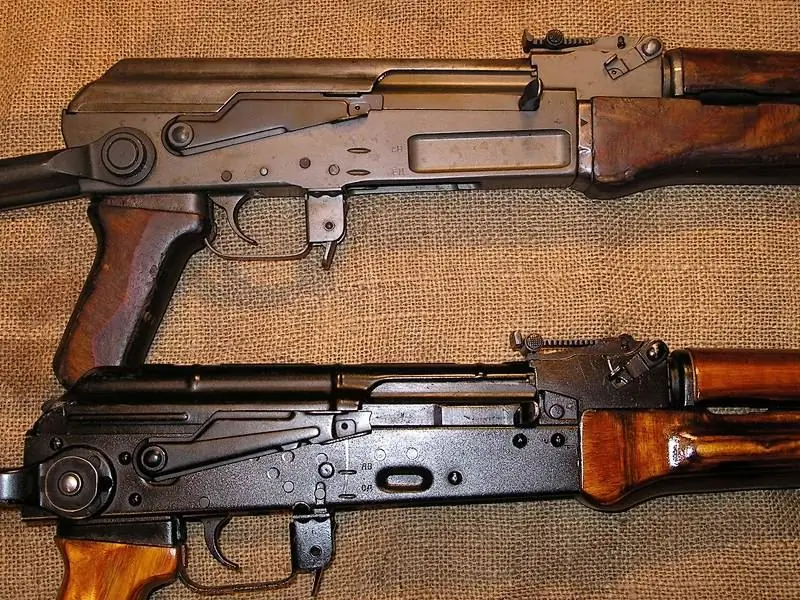
Ștampila 3. Datorită întârzierii tehnologice înnăscute (congenitale, inerente etc.) a industriei sovietice, nu a fost posibil să se stăpânească producția de cutii receptoare ștampilate, motiv pentru care acestea au trebuit realizate prin frezare din forjate, ceea ce a dus la o monstruoasă consumul de metal.
Dacă vorbim despre jena care i s-ar fi întâmplat lui Izhmash, care nu a reușit să reziste la calitatea necesară de „ștanțare”, atunci autorii acestor afirmații se află în această stare. Numele utilizatorilor încrezători, „experților”, analiștilor și altor cunoscători este o legiune, oamenii care nu numai că cunosc producția de construcții de mașini, ci și direct pe propria piele, cunosc gravitatea incredibilă a stăpânirii unei noi producții - câteva (Notă. Autorul articolului se referă la astfel de norocoși). Ce s-a întâmplat de fapt cu înlocuirea unei cutii ștampilate cu o cutie frezată în AK-47? Acordați atenție - doar cutiile, restul detaliilor nu au fost preocupate, dar concluzia se face pe o bază globală - asupra întregului „ștampilare” sovietic ca o tehnologie în ansamblu.
Să ne uităm mai întâi la construcție. Receptorul din AK nu este un suport de șuruburi frezat cu carcasă ștampilată, ca într-un furtun. Într-o pușcă de asalt germană, diferite piese ștampilate sunt responsabile pentru direcția suportului șurubului, pentru amplasarea magaziei și a suporturilor pentru optică, pentru localizarea pieselor de declanșare. Când le asamblați, este ușor să le potriviți cu un ciocan (acesta este un ciocan de lemn), în timp ce pierdeți interschimbabilitatea pieselor, așa cum au remarcat corect americanii. În pușca de asalt Kalashnikov, toate acestea sunt plasate într-o singură cutie ștampilată, cu un număr mare de piese suplimentare nituite, inclusiv căptușeala butoiului. Complexitatea sa nu uneori, ci un ordin de mărime mai mare decât receptorul Sturmgewer din două părți, dintre care doar una este ștampilată și nu are nicio funcție, cu excepția instalării pieselor de vizionare și a direcției suportului șurubului. În receptorul AK s-a realizat o bază și fixare fiabilă a magaziei. Într-o cutie ștampilată și fără a utiliza un arbore. Asta-i grozav.
Aici și mai jos, citate din cartea lui A. A. Malimona "Automate interne":
În perioada de pregătire pentru încercările militare, studiile efectuate la locul de testare au constatat că atunci când trageți dintr-o mitralieră cu accent pe magazie, precizia de tragere este de aproape 2,5 ori mai bună decât din mână.
Incapsularea AK (și SVD) a tuturor mecanicii funcționale într-o singură cutie și în același timp asigurarea accesului ușor la aceasta în timpul demontării incomplete și complete fără utilizarea instrumentelor este una dintre mai multe soluții inginerești excelente care împreună creează o capodoperă de proiectare a Kalashnikov pușcă de asalt. Soluții tehnice similare, atunci când toate funcționalitățile sunt asamblate într-un singur nucleu și, în același timp, asigură extinderea și dezvoltarea flexibilă a sistemului datorită interfețelor bine gândite, pot fi găsite în alte domenii, chiar și în programare. Desigur, depanarea unui astfel de nucleu al sistemului necesită mult mai mult timp (vezi declarația lui Guderian). Dar mai târziu, când a apărut un suport optic de încredere pe receptorul ștampilat, a apărut interschimbabilitatea pe capacul receptorului, a apărut un fund pliant lateral, a apărut lansatoare de grenade sub baril, a apărut un dispozitiv de întârziere a declanșatorului în interior, toate acestea nu au dus la o modificare semnificativă a tehnologia sau proiectarea mașinii (!) …
Un lot experimental de puști de asalt Kalashnikov a fost fabricat la Izhevsk Motozavod și trimis la teste pe teren, pe care nu le putea suporta. Printre comentarii au fost comentarii la receptor. După revizuire, arma a mers la procese militare și, în același timp, au început pregătirile pentru producție la Izhmash. Conform rezultatelor testelor militare, au fost aduse 228 modificări de proiectare (aproape două modificări pe o parte) și 114 tehnologice. Schimbarea simultană în proiectarea produsului și dezvoltarea instrumentelor pentru producerea acestuia nu mai reprezintă zahăr în sine. Dar sarcina a fost și mai abruptă, pe vechile pătrate, folosind o parte din vechile echipamente și nicidecum mașini de ștanțat de la compania Henel (care nu exista în natură), a fost creată o producție fără precedent cu volume de producție de peste jumătate de milion mașini pe an - oferind sfântul sfintelor ingineriei mecanice - interschimbabilitate … Și această producție a necesitat noi tehnologii, linii auto, care încă nu au fost create.
Fabrica avea o vastă experiență în dezvoltarea și producția în masă de arme de calibru mare și arme de tun, acumulate în timpul Marelui Război Patriotic, dar fabrica nu avea practică în producția de arme automate de calibru mediu. Proiectanții de fabricație și tehnologii, chimiștii și metalurgii au trebuit să-l achiziționeze în timpul stăpânirii unui nou produs.
Cu alte cuvinte, a fost necesar să se creeze o tehnologie care nu exista încă în lume, dar deocamdată a fost necesar să se folosească mașini învechite și echipamente universale, care aveau nevoie și de echipamente proprii, care trebuiau, de asemenea, proiectate și fabricate, și, cel mai important, era necesară eliberarea mașinilor.
La acea vreme, nu existau „ștampilări” germane, americane sau oricare alt străin, astfel încât să fie posibil să se înceapă imediat producerea unui produs care nu existase încă. Este destul de firesc să apară dificultăți în dezvoltarea producției. Stăpânirea producției este întotdeauna o soluție la un set de probleme care pot apărea oriunde, atât în etapa de producție, cât și ca urmare a utilizării în luptă a produselor. Primul lucru pe care trebuie să îl decideți este dacă soluția la problemă se află în defecte sau caracteristici de proiectare sau este tratată prin schimbarea proceselor tehnologice. Soluția poate să nu fie evidentă sau pot exista mai multe soluții.
În ambele cazuri, acest lucru necesită cercetări și experimentări suplimentare, colectarea și prelucrarea statisticilor - cheltuind cea mai valoroasă resursă - timpul. În total, în 1949 (anul în care a fost pusă în funcțiune pușca de asalt), au fost aduse 700 de modificări desenelor puștii de asalt și 20% din echipamentul de producție a fost modificat. În cele din urmă, există un alt factor - cel uman. Și nu vorbim despre sindromul înnăscut la nivel genetic „poate că va dispărea” și nu despre mâinile colecționarului tremurând de mahmureală, deși, cel mai probabil, așa le place celor care le place să speculeze despre „cultură” de producție „imaginați-vă acest lucru. În timp de război și chiar și acum, la o întreprindere de apărare, astfel de neajunsuri au fost tratate elementar. Este nevoie de timp pentru ca un lucrător să înceapă să producă produse de calitate și nu doar să facă, ci să facă multe și cu o calitate înaltă. În știința managementului, aceste fenomene sunt descrise prin curbe de „învățare” și „experiență”. Și mai există un factor, este puțin cunoscut datorită particularității sale. Particularitatea este că lucrătorul dezvoltă o abilitate care nu poate fi formalizată și descrisă în procesul tehnic. Voi da doar un exemplu din istoria stăpânirii producției de mitraliere Maxim la Izhevsk Motozavod. Centura de mitralieră, realizată conform desenelor și procesului tehnic obținut de la Tula, nu putea trece în niciun fel acceptarea militară. M-am impotmolit. A trebuit să zbor cu avionul din Tula fetele care adunau panglici la TOZ. Motivul sa dovedit a fi simplu - la asamblare, fetele au strâns ușor banda cu degetul.
În producție, a existat o ecranare mare a receptorului în ceea ce privește caracteristicile dimensionale și butoaiele pentru defecte în placarea cromată. Receptorul ștanțat-nituit nu avea rigiditatea necesară, datorită căreia, în timpul trecerii sale prin operațiile de prelucrare, s-a produs o distorsiune a dimensiunilor. De asemenea, nu avea rezistența necesară în îmbinările nituite ale carcasei și în locul de fixare a capului.
În timpul fabricării cutiei și a asamblării mașinii, a fost dezvăluită necesitatea unui număr mare de editări ale carcasei, a fost dificil să se asigure paralelismul ghidajelor cutiei cu axa butoiului, deformarea această parte a apărut și când s-a nituit sectorul fuse-translator.
Și asta în ciuda faptului că:
Volumul livrărilor de produse către client a fost strict programat nu numai pe trimestre, ci și pe luni, ceea ce, ținând cont de adevărata stare de fapt, a creat o anumită tensiune în activitatea de producție. Defecțiunile și neregulile la locul de muncă au fost cele mai tipice pentru perioada inițială de stăpânire a mașinii. Acestea au fost repetate periodic în viitor, ceea ce a dus la întreruperi în programul de furnizare a armelor, ceea ce a cauzat îngrijorări serioase din partea departamentului militar, deoarece reprezenta o amenințare la îndeplinirea planurilor ordinelor și la rearmarea în timp util. a armatei cu arme noi.
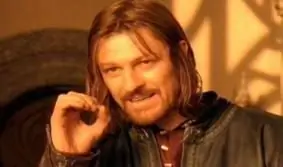
Aici nu puteți lua și asigura „paralelismul ghidajelor cutiei cu axa butoiului”, desenați desene ale pumnului și ale matricei, astfel încât după ce acestea sunt realizate și puse în producție, tensiunile reziduale din metal să nu începeți să o deformați la a cincea sau a șasea operație după ștanțare. Nu cu mult timp în urmă am făcut cunoștință cu industria turnătoriei. Turnarea este unică, adică aproape toate comenzile pentru piesele de dimensiuni mari diferă ca formă și dimensiune. În secolul al XXI-lea, s-au scris grămezi de monografii despre turnarea neferoasă, o mulțime de tabele și formule și mi s-a cerut să scriu un sistem expert în care băieții să introducă dimensiunile și configurația pieselor turnate, compoziții din aliaj, modurile de topire și turnare și rezultatele contracției metalice după dimensiune și locație, pentru a câștiga experiență și a calcula unghiurile de contracție în matrițele de injecție, ținând cont de căldurile din trecut. Metoda „poke științific” a fost și rămâne un mod de neîntrecut de a cunoaște lumea din jurul nostru pentru a o transforma în bine. Esența sa constă în colectarea, procesarea și analiza statisticilor, ceea ce duce treptat la găsirea soluției potrivite.
Sper că după ce am citit toate acestea, să fi apărut cel puțin o idee despre producția industrială pentru cei care nu au avut-o.
Războiul tocmai s-a încheiat, care a necesitat eforturi fizice și morale fără precedent pentru a stăpâni noi tipuri de arme și o creștere multiplă a producției. Și iată o nouă provocare. În condiții de presiune de timp sălbatic, atunci când este necesar să eliberați arme, îndeplinind planul de aprovizionare, când proiectarea acestuia se schimbă în mod constant, când în unele probleme există nu numai experiența noastră proprie, ci și mondială, se ia singura decizie corectă - o tranziție temporară la o carcasă de receptor frezată. Acesta este un pas complet de înțeles, care nu subminează în niciun fel calificările tehnice sau profesionale ale acelor designeri și tehnologi care au creat gloria mitralierei sovietice. Dar orice mențiune a acestui fapt în zadar fără a aduce un omagiu faptului muncitor al acestor oameni, cel puțin, este pur și simplu lipsită de respect pentru ei.
Literatură și surse:
Dieter Handrich, Sturmgewehr 44.
Dr. Dieter Kappell, Sturmgewer-Patrone 7, 92x33
Norbert Moczarski, Die Ära der Gebrüder Schmeisser in der Waffenfabrik Fa. C. G. Haenel Suhl 1921-1948
A. S. Iușcenko, mitraliere proiectate de A. I. Sudaev
Din istoria afacerilor cu arme. Rezumat de articole. Muzeul Kalashnikov
M. T. Kalashnikov, Note ale unui proiectant de arme
A. A. Malimon, mitraliere interne (note ale unui producător de arme)
D. F. Ustinov, În numele victoriei
V. N. Novikov. În ajun și în zilele încercărilor
B. L. Vannikov, Note ale comisarului poporului
Și, de asemenea, cărți de Fedorov, Bolotin, Monetchikov, Nagaev, Chumak etc.