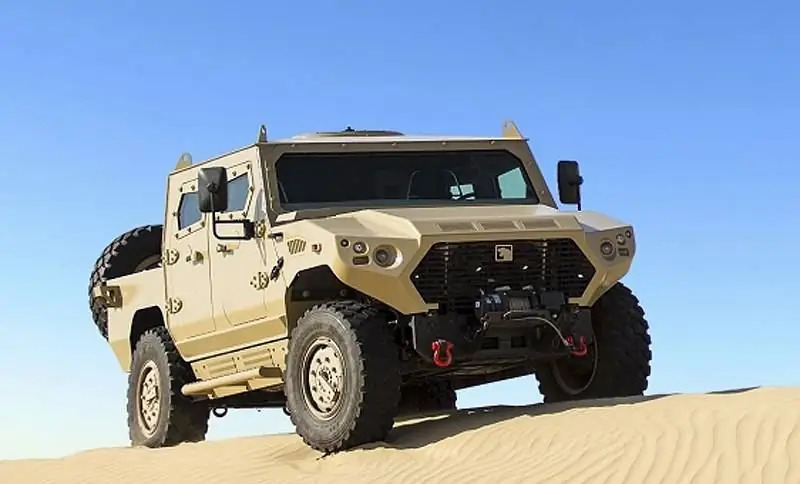
Armura este cu milioane de ani mai veche decât omenirea și s-a dezvoltat în primul rând pentru a proteja împotriva fălcilor și ghearelor. Este posibil ca crocodilii și broaștele țestoase să inspire parțial oamenii să creeze elemente de protecție. Toate armele de energie cinetică, fie că este un club preistoric sau un proiectil care străpunge armura, sunt concepute pentru a concentra o forță mare într-o zonă mică, sarcina sa este de a pătrunde în țintă și de a-i provoca daune maxime. În consecință, sarcina armurii este de a preveni acest lucru prin devierea sau distrugerea mijloacelor de atac și / sau dispersarea energiei de impact pe o zonă cât mai mare posibil, pentru a minimiza orice daune aduse forței de muncă, sistemelor de transport și structurilor pe care le protejează.
Armura modernă constă de obicei dintr-un strat exterior dur pentru a opri, devia sau distruge proiectilul, un strat intermediar cu un „lucru de rupt” foarte ridicat și un strat interior vâscos pentru a preveni crăpăturile și resturile.
Oţel
Oțelul, care a devenit primul material utilizat pe scară largă la crearea vehiculelor blindate, este încă în căutare, în ciuda apariției armurilor bazate pe aliaje ușoare de aluminiu și titan, ceramică, compozite cu o matrice polimerică, armate cu fibre de sticlă, aramidă și polietilenă cu greutate moleculară foarte ridicată, precum și materiale compozite cu matrice metalică.
Multe fabrici de oțel, inclusiv SSAB, continuă să dezvolte oțeluri de înaltă rezistență pentru o varietate de aplicații critice pentru greutate, cum ar fi învelișul suplimentar. Armatura de oțel blindată ARM OX 600T, disponibilă cu grosimi de 4-20 mm, este disponibilă cu o duritate garantată de 570 până la 640 unități HBW (prescurtare pentru Duritate, Brinell, Wolfram; un test în care este presată o bilă de tungsten cu un diametru standard într-un eșantion de material cu o forță cunoscută, atunci se măsoară diametrul adânciturii formate; apoi acești parametri sunt înlocuiți în formulă, care vă permite să obțineți numărul de unități de duritate).
SSAB subliniază, de asemenea, importanța realizării echilibrului corect de duritate și duritate pentru penetrare și protecție la explozie. La fel ca toate oțelurile, ARMOX 600T este compus din fier, carbon și o serie de alte componente de aliere, inclusiv siliciu, mangan, fosfor, sulf, crom, nichel, molibden și bor.
Există restricții privind tehnicile de fabricație utilizate, mai ales când vine vorba de temperatură. Acest oțel nu este destinat tratamentului termic suplimentar; dacă este încălzit peste 170 ° C după livrare, SSAB nu își poate garanta proprietățile. Companiile care pot evita acest tip de restricție sunt susceptibile de a atrage controlul atent al producătorilor de vehicule blindate.
O altă companie suedeză, Deform, oferă producătorilor de vehicule blindate piese din oțel blindat rezistent la glonț, în special celor care doresc să îmbunătățească protecția vehiculelor comerciale / civile.
Firewall-urile Deform dintr-o singură piesă sunt instalate în Nissan PATROL 4x4, microbuzul Volkswagen T6 TRANSPORTER și camioneta Isuzu D-MAX, împreună cu o foaie solidă din același material. Procesul de formare la cald dezvoltat de Deform și utilizat în producția de foi menține o duritate de 600 HBW.
Compania susține că poate restabili proprietățile tuturor oțelurilor blindate de pe piață, menținând în același timp o formă definită structural, în timp ce piesele rezultate sunt mult superioare structurilor sudate tradiționale și parțial suprapuse. În metoda dezvoltată de Deform, foile sunt stinse și călite după forjare la cald. Datorită acestui proces, este posibil să se obțină forme tridimensionale care nu pot fi obținute prin formarea la rece fără obligatorii în astfel de cazuri „suduri care încalcă integritatea punctelor critice”.
Plăcile de oțel deformate la cald au fost utilizate pe BAE Systems BVS-10 și CV90 și, de la începutul anilor 1990, pe multe mașini Kraus-Maffei Wegmann (KMW). Comenzile vin pentru producția de plăci de blindaj tridimensional pentru rezervorul LEOPARD 2 și mai multe plăci în formă pentru vehiculele BOXER și PUMA, plus pentru mai multe vehicule Rheinmetall, inclusiv din nou BOXER, precum și o trapă pentru vehiculul WIESEL. Deform funcționează și cu alte materiale de protecție, inclusiv aluminiu, kevlar / aramid și titan.
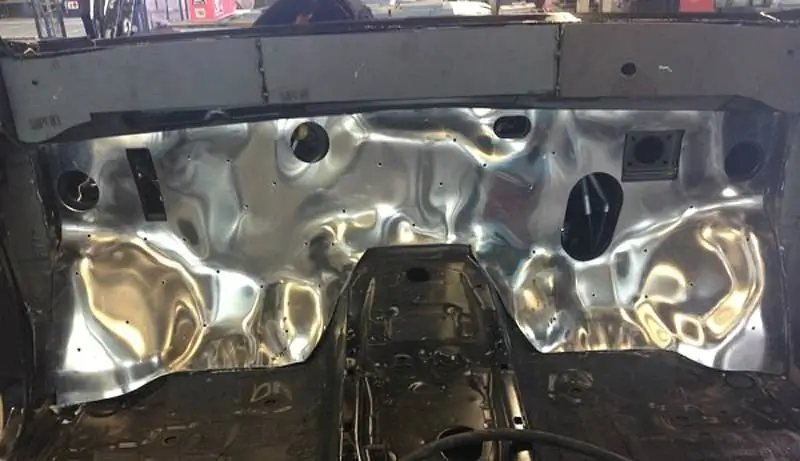
Progresul din aluminiu
În ceea ce privește vehiculele blindate, pentru prima dată armura din aluminiu a fost utilizată pe scară largă la fabricarea transportorului blindat M113, care a fost produs din 1960. Era un aliaj, desemnat 5083, care conținea 4,5% magneziu și cantități mult mai mici de mangan, fier, cupru, carbon, zinc, crom, titan și altele. Deși 5083 își păstrează bine rezistența după sudare, nu este un aliaj tratabil termic. Nu are o rezistență la fel de bună la gloanțele de perforare a armurii de 7,62 mm, dar, după cum au confirmat testele oficiale, oprește gloanțele de perforare a armurii în stil sovietic de 14,5 mm mai bine decât oțelul, economisind în același timp greutatea și adăugând puterea dorită. Pentru acest nivel de protecție, foaia de aluminiu este mai groasă și de 9 ori mai puternică decât oțelul cu o densitate mai mică de 265 r / cm3, ceea ce duce la o reducere a greutății structurii.
În curând, producătorii de vehicule blindate au început să solicite armuri din aluminiu mai ușoare, mai rezistente din punct de vedere balistic, sudabile și tratabile termic, ceea ce a dus la dezvoltarea lui Alcan din 7039 și mai târziu din 7017, ambele cu un conținut mai ridicat de zinc.
La fel ca în cazul oțelului, ștanțarea și asamblarea ulterioară pot afecta negativ proprietățile de protecție ale aluminiului. La sudare, zonele afectate de căldură se înmoaie, dar rezistența lor este parțial restabilită din cauza întăririi în timpul îmbătrânirii naturale. Structura metalului se schimbă în zonele înguste din apropierea sudurii, creând tensiuni reziduale mari în caz de erori de sudură și / sau asamblare. În consecință, tehnicile de fabricație ar trebui să le minimizeze, în timp ce riscul de fisurare prin coroziune la stres ar trebui, de asemenea, redus la minimum, mai ales atunci când durata de viață a mașinii este de așteptat să fie mai mare de trei decenii.
Cracarea prin coroziune prin stres este un proces de apariție și creștere a fisurilor într-un mediu coroziv, care tinde să se deterioreze pe măsură ce crește numărul elementelor de aliere. Formarea fisurilor și creșterea lor ulterioară are loc ca urmare a difuziei hidrogenului de-a lungul limitelor granulelor.
Determinarea susceptibilității la fisurare începe cu extragerea unei cantități mici de electroliți din fisuri și analiza acestuia. Se efectuează teste de coroziune la solicitare cu viteză redusă pentru a determina cât de grav a fost deteriorat un anumit aliaj. Întinderea mecanică a două eșantioane (una într-un mediu coroziv, iar cealaltă în aer uscat) are loc până când acestea cedează, iar apoi se compară deformarea plastică la locul fracturii - cu cât eșantionul este mai întins până la eșec, cu atât mai bine.
Rezistența la fisurare prin coroziune prin stres poate fi îmbunătățită în timpul prelucrării. De exemplu, potrivit Total Materia, care se numește „cea mai mare bază de date din lume de materiale”, Alcan a îmbunătățit performanța 7017 în testele de coroziune la stres accelerat de 40 de ori. Rezultatele obținute fac, de asemenea, posibilă dezvoltarea metodelor de protecție împotriva coroziunii pentru zonele structurilor sudate, în care este dificil să se evite tensiunile reziduale. Cercetările care vizează îmbunătățirea aliajelor pentru a optimiza caracteristicile electrochimice ale îmbinărilor sudate sunt în curs de desfășurare. Lucrările la noi aliaje tratabile la căldură se concentrează pe îmbunătățirea rezistenței și rezistenței la coroziune, în timp ce lucrările la aliajele care nu sunt tratabile termic vizează eliminarea constrângerilor impuse de cerințele de sudabilitate. Cele mai dure materiale din dezvoltare vor fi cu 50% mai puternice decât cea mai bună armură din aluminiu utilizată astăzi.
Aliajele cu densitate scăzută, cum ar fi aluminiul cu litiu, oferă economii de greutate de aproximativ 10% față de aliajele anterioare cu rezistență comparabilă la glonț, deși performanța balistică nu a fost încă evaluată pe deplin conform Total Materia.
Metodele de sudare, inclusiv cele robotizate, se îmbunătățesc, de asemenea. Printre sarcinile rezolvate se numără minimizarea alimentării cu căldură, un arc de sudură mai stabil datorită îmbunătățirii sistemelor de alimentare cu energie și sârmă, precum și monitorizarea și controlul procesului de către sisteme expert.
MTL Advanced Materials a lucrat cu ALCOA Defense, un renumit producător de plăci de blindaj din aluminiu, pentru a dezvolta ceea ce compania descrie ca un „proces de formare la rece fiabil și repetabil”. Compania remarcă faptul că aliajele de aluminiu dezvoltate pentru aplicații de armură nu au fost proiectate pentru formarea la rece, ceea ce înseamnă că noul său proces ar trebui să ajute la evitarea modurilor comune de defecțiune, inclusiv a fisurilor. Scopul final este de a permite proiectanților de mașini să minimizeze nevoia de sudare și să reducă numărul de piese, potrivit companiei. Reducând volumul de sudură, compania subliniază, crește rezistența structurală și protecția echipajului, reducând în același timp costurile de producție. Începând cu aliajul bine dovedit 5083-H131, compania a dezvoltat un proces de formare la rece a pieselor cu un unghi de îndoire de 90 de grade de-a lungul și peste granule, apoi a trecut la materiale mai complexe, de exemplu, aliajele 7017, 7020 și 7085, obținând și rezultate bune.
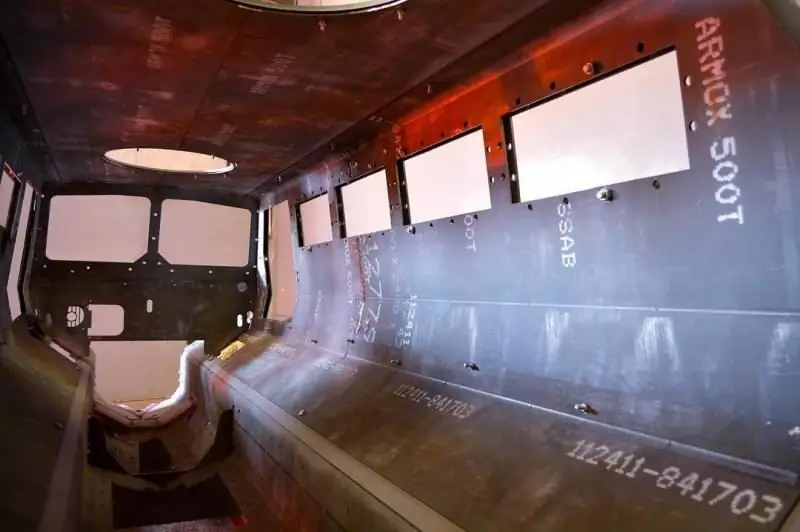
Ceramică și compozite
Cu câțiva ani în urmă, Morgan Advanced Materials a anunțat dezvoltarea mai multor sisteme de armură SAMAS, care constau dintr-o combinație de ceramică avansată și compozite structurale. Linia de produse include armuri articulate, căptușeli anti-fragmentare, capsule de supraviețuire realizate din compozite structurale pentru înlocuirea corpurilor metalice și protejarea modulelor de armă, atât locuite, cât și nelocuite. Toate acestea pot fi adaptate la cerințe specifice sau pot fi făcute la comandă.
Oferă protecție STANAG 4569 Nivelul 2-6, împreună cu performanțe multi-impact și economii de greutate (compania susține că aceste sisteme cântăresc la jumătate din produsele din oțel similare) și se adaptează la amenințări, platforme și misiuni specifice … Căptușelile anti-așchiere pot fi realizate din panouri plate cântărind 12,3 kg pentru a acoperi o suprafață de 0,36 m2 (aproximativ 34 kg / m2) sau fitinguri solide cu o greutate de 12,8 kg pentru 0,55 m2 (aproximativ 23,2 kg / m2).
Potrivit Morgan Advanced Materials, armura suplimentară concepută pentru modernizarea și modernizarea platformelor existente oferă aceleași capacități la jumătate din greutate. Sistemul brevetat oferă o protecție maximă împotriva unei game largi de amenințări, inclusiv arme de calibru mic și mediu, dispozitive explozive improvizate (IED) și grenade cu rachetă, precum și performanțe cu impact multiplu.
Un sistem de armură "semi-structural" cu o bună rezistență la coroziune este oferit pentru modulele de armă (în plus față de aplicațiile aeriene și maritime) și, împreună cu economisirea greutății și minimizarea problemelor cu centrul de greutate, spre deosebire de oțel, creează mai puține probleme de compatibilitate electromagnetică.
Protecția modulelor de arme este o problemă specială, deoarece acestea sunt o țintă atractivă, deoarece dezactivarea lor afectează drastic controlul situației de către echipaj și capacitatea vehiculului de a face față amenințărilor din apropiere. De asemenea, au optoelectronică delicată și motoare electrice vulnerabile. Deoarece sunt de obicei instalate în partea de sus a vehiculului, blindajul trebuie să fie ușor pentru a menține centrul de greutate cât mai jos posibil.
Sistemul de protecție a modulelor de arme, care poate include sticlă blindată și protecție a părții superioare, este complet pliabil, două persoane îl pot reasambla în 90 de secunde. Capsulele de supraviețuire compozite sunt fabricate din ceea ce compania descrie ca „materiale unice dure și formulări polimerice”, acestea asigură protecție împotriva șrapnelelor și pot fi reparate pe teren.
Protecția soldatului
Sistemul SPS (Soldier Protection System) dezvoltat de 3M Ceradyne include căști și inserții în armură pentru sistemul integrat de protecție a capului (IHPS) și VTP (Vital Torso Protection) - componente ESAPI (Enhanced Small Arms Protective Insert) - insert îmbunătățit pentru protecție împotriva arme mici) ale sistemului SPS.
Cerințele IHPS includ o greutate mai mică, o protecție pasivă a auzului și o protecție îmbunătățită a impactului contondent. Sistemul include, de asemenea, accesorii, cum ar fi o componentă pentru protejarea maxilarului inferior al unui soldat, o vizieră de protecție, un suport pentru ochelari de vedere nocturnă, ghidaje pentru, de exemplu, lanternă și cameră și protecție modulară suplimentară împotriva glonțului. Contractul, în valoare de peste 7 milioane de dolari, prevede furnizarea a aproximativ 5.300 de căști. Între timp, peste 30.000 de seturi ESAPI - inserții mai ușoare pentru armura corporală - vor fi livrate în baza contractului de 36 de milioane de dolari. Producția ambelor kituri a început în 2017.
Tot în cadrul programului SPS, KDH Defense a selectat materialele SPECTRA SHIELD și GOLD SHIELD ale lui Honeywell pentru cinci subsisteme, inclusiv subsistemul Tors și Extremity Protection (TEP) care urmează să fie furnizat pentru proiectul SPS. Sistemul de protecție TEP este cu 26% mai ușor, ceea ce reduce în final greutatea sistemului SPS cu 10%. KDH va utiliza SPECTRA SHIELD, care se bazează pe fibră UHMWPE, și GOLD SHIELD, pe bază de fibre de aramidă, în propriile produse pentru acest sistem.
Fibra SPECTRA
Honeywell folosește un proces propriu de filare și extragere a fibrelor polimerice pentru a încorpora materia primă UHMWPE în fibra SPECTRA. Acest material este de 10 ori mai puternic decât oțelul în ceea ce privește greutatea, rezistența sa specifică este cu 40% mai mare decât cea a fibrei de aramidă, are un punct de topire mai mare decât polietilena standard (150 ° C) și o rezistență mai mare la uzură comparativ cu alți polimeri, pentru exemplu, poliester.
Materialul SPECTRA puternic și rigid prezintă o deformare ridicată la rupere, adică se întinde foarte puternic înainte de rupere; această proprietate permite absorbirea unei cantități mari de energie de impact. Honeywell susține că compozitele din fibre SPECTRA au performanțe foarte bune la impacturi de mare viteză, cum ar fi gloanțele puștii și undele de șoc. Potrivit companiei, „Fibra noastră avansată reacționează la impact eliminând rapid energia cinetică din zona de impact … are, de asemenea, o bună amortizare a vibrațiilor, o bună rezistență la deformări repetate și caracteristici excelente de frecare internă a fibrelor, împreună cu o rezistență excelentă la substanțe chimice., apă și lumină UV."
În tehnologia sa SHIELD, Honeywell răspândește fire paralele de fibre și le leagă impregnându-le cu o rășină avansată pentru a crea o panglică unidirecțională. Apoi straturile acestei benzi sunt plasate transversal la unghiurile dorite și la o temperatură și presiune date, lipite într-o structură compozită. Pentru aplicații ușor de purtat, este laminat între două straturi de film transparent subțire și flexibil. Deoarece fibrele rămân drepte și paralele, disipă energia de impact mai eficient decât dacă ar fi țesute într-o țesătură.
Short Bark Industries folosește și SPECTRA SHIELD în bodyguardul BCS (Ballistic Combat Shirt) pentru sistemul SPS TEP. Short Bark este specializat în protecție moale, îmbrăcăminte tactică și accesorii.
Potrivit lui Honeywell, soldații au ales elemente de protecție fabricate din aceste materiale după ce au demonstrat performanțe superioare față de omologii lor din fibră de aramidă.