Patriotismul elitei industriale sovietice a fost combinat cu responsabilitatea comună pentru rezultatul final
Interacțiunea interindustrială în orice moment - atât în Imperiul Rus, cât și în URSS, și astăzi - nu aparținea punctelor forte ale industriei interne. Spre deosebire de Germania sau Statele Unite, unde obligațiile contractuale aveau și au o forță imuabilă și aproape sacră.
Să luăm, de exemplu, relația dintre metalurgii ruși și constructorii de mașini. În a doua jumătate a secolului al XIX-lea, noile fabrici de inginerie de transport și șantierele navale nu au primit cantitatea necesară de metale industriale de la minerii din Ural. Acesta din urmă a considerat că nu este rentabil să producă o mulțime de produse laminate relativ ieftine, deoarece același profit a fost asigurat de un volum mult mai mic de fier scump pentru acoperișuri. Metalul lipsă pentru axele auto, arborii motorului și pielea navei trebuia achiziționat în străinătate. Abia până la sfârșitul secolului, problema a fost rezolvată de uzinele metalurgice din sudul Rusiei, fondate de industriași belgieni sau francezi. În Ural, francezii au construit și o plantă - Chusovskaya.
S-ar părea că, în epoca sovietică, astfel de capricii erau excluse. În plus, uzinele metalurgice construite în anii 30 au furnizat țării metalul în ansamblu. Cu toate acestea, de fiecare dată când constructorii de mașini au solicitat noi tipuri complexe de produse laminate, metalurgienii le-au stăpânit ani de zile sau chiar decenii.
Feudalismul departamental
Să ne întoarcem la istoria lui Uralvagonzavod. Deja în primele sale proiecte, a fost planificată utilizarea roților din oțel laminate solid sub mașinile cu patru osii, deoarece capacitatea de proiectare a atins capacitatea sa de proiectare, al cărei furnizor a fost planificat pentru uzina metalurgică din apropiere de Novo-Tagil. Cu toate acestea, acesta din urmă a fost construit de către departamentul metalurgic și a amânat construcția laminorului cu roți în 1938-1942 și nu în primul rând. Drept urmare, cazul nu a început înainte de război. Și după război, închirierea roților nu a fost prea interesată de metalurgieni. Rezultat: până la mijlocul anilor '50, mașinile Tagil au părăsit fabrica pe roți din fontă de scurtă durată în loc de roți din oțel. Acest lucru a adus pierderi uriașe muncitorilor feroviari, dar nu a existat nicio alegere: fie astfel de mașini, fie niciuna.
Același lucru s-a întâmplat cu introducerea oțelurilor slab aliate în construcția de transport. Au promis o reducere semnificativă a greutății moarte a materialului rulant, menținând în același timp toate caracteristicile de performanță. Proiectanții Uralvagonzavod au început să proiecteze mașini din metal cu aliaj scăzut la sfârșitul anilor 30, dar producția lor în serie a început abia în a doua jumătate a anilor 50, deoarece metalurgienii nu furnizau nici produse laminate corespunzătoare, nici feroaliaje pentru piesele turnate.
Trebuie spus că virusul feudalismului departamental a afectat ei înșiși constructorii de mașini. În vara anului 1937, a avut loc o poveste interesantă care a caracterizat relațiile interinstanțiale din acea vreme. Direcția principală a întreprinderilor metalurgice a trimis la Uralvagonzavod o comandă pentru cinci mii de tone de semifabricate pentru fabrica de bandaj recent lansată a uzinei Novo-Tagil. Direcția principală a ingineriei transporturilor a fost revoltată de încălcarea unei întreprinderi subordonate. Șef adjunct al Direcției principale G. G. Pe 11 iulie, Aleksandrov a trimis o scrisoare către GUMP și Uralvagonzavod cu următoarea declarație: „Suntem extrem de surprinși că soluția unei probleme atât de importante, precum organizarea producției unui bandaj gol la Uralvagonzavod, a fost efectuată fără participarea noastră și cu atât mai mult - nici măcar nu ni s-a trimis o copie a ținutei trimise lui Uralvagonzavod … Vă rog să stabiliți o procedură fermă pentru emiterea de semifabricate fabricilor noastre numai prin acord cu noi și prin Glavtransmash."
Drept urmare, metalurgienilor li s-a refuzat bandajul de oțel, presupus din cauza imposibilității tehnice de a arunca lingouri de înaltă calitate în atelierul deschis din Uralvagonzavod. Între timp, deja în 1936, aici a fost turnat un semifabricat axial, iar în 1937 - lingouri pentru laminarea foilor. Prin urmare, lingourile pentru moara de giulgi, situată la câțiva kilometri de UVZ, trebuiau transportate din uzinele Vyksa și Kuznetsk. Mai mult, calitatea lor a lăsat mult de dorit, iar volumele de aprovizionare au fost insuficiente.
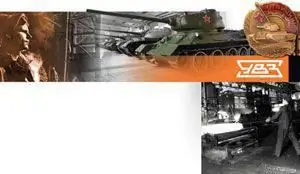
În 1938, istoria s-a repetat. Principalul consumator de lingouri UVZ a fost uzina de artilerie Molotov (adică Perm), care a primit un lot de semifabricate la sfârșitul anului. Și doar un număr mic dintre aceștia au mers la magazinul de bandaje, care a trebuit să importe din nou metalul lipsă pentru doi, doi și jumătate de mii de kilometri. Interesele industriei în distribuția oțelului Uralvagonzavodsk au dominat în mod clar.
Nici boala departamentală nu a scutit industria de apărare. Numeroase publicații despre istoria construcției de tancuri sovietice sunt de-a dreptul pline de exemple despre modul în care construcția prototipurilor sau desfășurarea producției de masă a fost întârziată din cauza nelivrării metalului, în special a armurilor.
Și chiar și astăzi interesul sectorial nu a plecat nicăieri, ci doar și-a schimbat forma. Cererile pentru noi forme de produse laminate sunt pur și simplu combătute cu prețuri exorbitante. Nu este nevoie să vorbim despre o politică coordonată. După prăbușirea cursului de schimb al rublei la începutul anilor 2014-2015, companiile metalurgice au ridicat prețurile la materialul rulant cu 30-60 la sută. Și au început imediat să se plângă de constructorii de mașini pentru echipamentele care au crescut în preț - până la urmă, mașinile sunt produse în Rusia și nu sunt legate de cursul de schimb al dolarului.
Se pare că în țara noastră există un singur remediu pentru problemele intersectoriale: crearea de sisteme integrate vertical, în care minereul minat de propriile forțe este transformat mai întâi în metal și apoi în mașini finite.
Unitatea în timpul războiului
Cu toate acestea, există o scurtă perioadă în istoria noastră când interesele industriei s-au retras în plan secund. Vorbim despre Marele Război Patriotic. Patriotismul neîndoielnic al elitei industriale sovietice de atunci era combinat cu responsabilitatea comună a tuturor celor implicați în producția de apărare pentru rezultatul final. Adică, directorul fabricii blindate de rulare era responsabil nu atât pentru volumul de oțel topit și laminat, cât și pentru numărul de tancuri construite.
Pasul principal în această direcție a fost făcut de directorul NII-48 A. S. Zavyalov. În primele zile ale războiului, s-a adresat guvernului cu o propunere de a instrui institutul să introducă tehnologii pentru producerea oțelurilor speciale și a structurilor blindate la întreprinderile din estul țării, care au fost implicate pentru prima dată în fabricarea armăturilor blindate. vehicule. La începutul lunii iulie, echipe de specialiști din NII-48 au condus restructurarea tehnologică a celor mai mari 14 întreprinderi. Printre acestea s-au numărat uzinele metalurgice Magnitogorsk și Kuznetsk, Uzinele metalurgice Novo-Tagil și Chusovka, Uzina grea de construcție a mașinilor Ural, Uzina Gorky Krasnoye Sormovo, Uzina de tractoare Stalingrad, Octombrie roșu Stalingrad și nr. 264. Astfel, Zavyalov a încălcat tabu de dinainte de război: lista includea întreprinderi ale comisariatelor a trei persoane.
Patriotismul și suprimarea obligatorie a egoismului departamental au oferit metalurgiei sovietice rate de dezvoltare fără precedent a produselor de apărare, nici în perioada pre-război, nici în cea postbelică. În câteva luni, în estul țării (în principal în Ural), a fost organizată producția de feromanganez, ferosilicon, ferocrom, ferrovanadiu și alte aliaje, fără de care este imposibil să se obțină oțel blindat. După pierderea regiunilor de vest, Chelyabinsk a rămas singura fabrică de feroaliaje din URSS. Pe el, în scurt timp, topirea a fost mărită de două ori și jumătate. Au fost produse 25 de tipuri de produse, dar mai ales erau din diferite tipuri de ferocrom. Topirea feromanganei a fost stabilită în furnalele și nu numai în furnalele vechi cu tonaj redus ale uzinelor Nizhniy Tagil și Kushvinsky, ci și într-un cuptor modern modern al combinatului Magnitogorsk. Contrar tuturor ideilor dinaintea războiului, ferocromul a fost topit în a doua jumătate a anului 1941 în furnalele lor de către metalurgii din uzinele Nizhniy Tagil și Serov, iar oamenii de știință din filiala Ural a Academiei de Științe a URSS au oferit o mare asistență în crearea unui nou tehnologie. Mai târziu, topirea cu ferosilicon a fost stăpânită în furnalele Serov.
Nu existau tabere blindate nici în Ural, nici în Siberia de Vest înainte de război, acestea trebuind să fie transferate în grabă de la întreprinderi aflate în zona de luptă.
În vara anului 1941, echipamentul evacuat era încă în tranzit. Și apoi mecanicul șef al combinației Magnitogorsk N. A. Ryzhenko a sugerat rularea armurii pe o moară înflorită. În ciuda riscului mare, ideea a fost realizată. Și în octombrie, a intrat în funcțiune o tabără blindată, scoasă din uzina Mariupol. A fost asamblat în doar 54 de zile. Conform standardelor de dinainte de război, acest lucru a durat un an.
Fabrica Novo-Tagil a luat tabăra de la Leningrad. Pregătirile pentru admitere au început în iulie, inițial s-a presupus că va fi montat pe locul bandajului. Tabăra de bandaj a fost dezasamblată, dar s-a dovedit că vechiul stoc nu era suficient pentru a instala tabăra blindată și trebuia plasat în altă parte. Războiul a forțat să facă ceea ce a fost considerat imposibil până de curând: în urmă cu doar un an, încercările de a realiza construcții industriale printr-o metodă integrată „de mare viteză” în Nijni Tagil au avut cel mult un succes parțial, iar în vara anului 1941 cele mai multe operațiunea de construcție complexă a fost aproape perfectă. Pe 10 septembrie, prima foaie de oțel Tagil a fost rulată cu o lună înainte de termen. În total, până la sfârșitul anului, au fost obținute 13.650 de tone de tablă, inclusiv aproximativ 60% din armură (moara a fost testată pe oțel carbon, iar în octombrie - decembrie, oțelul carbon a fost laminat cu o lipsă de lingouri de armură). Drept urmare, deja în ianuarie 1942, producția lunară de plăci de armură la fabricile din Ural a depășit șase luni în întreaga Uniune Sovietică de dinainte de război.
Nu au avut loc evenimente mai puțin surprinzătoare la alte întreprinderi puțin cunoscute. În timpul războiului, uzina metalurgică Zlatoust a fost inferioară combinației Magnitogorsk din punct de vedere al volumului de topire și al oțelului laminat, dar a depășit-o în mod semnificativ în amestecul său de produse - aici s-au produs aproximativ 300 de clase de aliaj și oțel carbon. Fără aprovizionarea de la Zlatoust, producția multor tipuri de arme, în principal motoare cu tanc, s-ar fi oprit.
Vechile fabrici Ural s-au dovedit a fi indispensabile în producția de loturi mici de oțel de înaltă calitate. De exemplu, metalul de la Serov Metallurgical, principalul producător de produse laminate calibrate, a fost investit în fiecare tanc sovietic. Fabrica de la Nizhnesalda a trecut la topirea fierului de nichel și a oțelului. Această listă poate fi continuată la nesfârșit - în timpul războiului, oriunde a existat cel puțin o cupolă, s-a topit metalul de calitate pentru arme.
Există o poveste curioasă cu fluxuri pentru sudarea automată. Înainte și la începutul războiului, au fost topite la una dintre întreprinderile din Donbass, după ocuparea căreia proviziile centralizate s-au oprit complet. La sfârșitul anului 1941, angajații Institutului de sudare electrică al Academiei de Științe din RSS ucraineană au început să caute materiale de substituție disponibile în Ural într-o stare mai mult sau mai puțin utilizabilă. Și i-au găsit - sub formă de zgură de furnal din uzina metalurgică Ashinskiy. Au fost necesare doar mici îmbunătățiri: furnalele și-au îmbogățit zgurile cu mangan și le-au transformat astfel într-un flux complet adecvat. Echipamentul necesar testării a fost adus de la Nizhny Tagil direct la Asha.
Exemple de cooperare locală între tancuri și instalații metalurgice sunt foarte indicative. Înainte de lansarea propriilor instalații, la uzina metalurgică Nizhniy Tagil a fost efectuată tratarea termică a părților rezervorului uzinei de rezervoare Ural nr. 183.
Munca de succes a lucrătorilor de turnătorie UTZ a fost mult facilitată de asistența fabricii vecine Nizhniy Tagil, care a stabilit producția de dopuri de silex refractare de înaltă calitate. Acest lucru a făcut posibilă executarea turnării fără probleme a topiturilor de oțel blindat greu pentru turnarea în formă.
În 1942-1945, cuptoarele cu focar deschis de la UTZ funcționau în principal pe cuptorul cu cocs și gazul din furnalul de la uzinele de cocs Novo-Tagil Metalurgical și Nizhniy Tagil. Conducta de gaz funcționează din februarie 1942. Stația proprie de producere a gazului fabricii nr. 183 a asigurat nu mai mult de 40% din necesități.
Uneori, un sfat simplu a fost suficient pentru a rezolva o problemă. Informațiile metalurgienilor locali despre o mică mină de mangan dezvoltată în anii 1870 au contribuit la supraviețuirea cu câteva săptămâni înainte de începerea livrărilor de feromanganez fără a opri turnarea șinelor de tancuri.
Un alt exemplu: pe măsură ce producția de oțel blindat a crescut, atelierul deschis nu mai putea ține pasul cu topirea metalului pentru capetele bombelor aeriene. Nu era posibil să-l obții din exterior. Directorul Yu. E. Maksarev a reamintit cursul evenimentelor ulterioare din memoriile sale: „Când eram la una dintre ședințele din comitetul orașului, m-am întâlnit cu directorul vechii fabrici Demidov și am cerut să iau de la mine capul bombei. El a spus: Nu pot ajuta cu oțelul, dar cu sfaturi voi ajuta. Și când am venit la fabrica lui, mi-a arătat un convertor Bessemer de o tonă și jumătate cu suflare medie. Mi-a dat desenele și mi-a spus că știe că avem o turnătorie bună de fier mecanizat, iar convertoarele dvs. se vor sudura”. Așa a apărut comanda pentru uzina din 8 septembrie 1942 în organizația din magazinul de roți Griffin din secțiunea Bessemer a trei convertoare mici (câte o tonă și jumătate de metal fiecare). Până la 25 septembrie, proiectul a fost pregătit de departamentul de proiectare și tehnologie al conducerii construcțiilor de capital, specialiștii departamentului mecanic șef au sudat rapid convertoare și cazane - rezervoare de stocare a fierului lichid. Testul departamentului Bessemer și distribuirea unui lot experimental de cinci nume de piese au avut loc la începutul lunii octombrie-noiembrie 1942. Producția în serie a început la sfârșitul lunii noiembrie.
La sfârșitul subiectului: cooperarea metalurgilor și a constructorilor de tancuri în timpul războiului a acționat în ambele direcții. Instalatorii uzinei de rezervoare Ural au participat la punerea în funcțiune a multor unități noi ale uzinei metalurgice Novo-Tagil. În mai 1944, un număr semnificativ de plăci de căptușeală pentru repararea furnalului au fost fabricate în atelierul de turnare cu turn blindat.
Dar asistentul principal al metalurgilor a fost, desigur, uzina de construcție a mașinilor grele din Ural. Cărțile comenzilor pentru UZTM pentru anii 1942-1945 sunt literalmente ambalate cu documente privind producția de piese de schimb și dispozitive în scopuri metalurgice - atât pentru nevoile industriei de tancuri, cât și pentru întreprinderile Comisariatului Popular al Metalurgiei Feroase. În toamna anului 1942, la UZTM a fost restaurată oficial o divizie specială pentru producția de echipamente pentru uzinele metalurgice. Acesta a primit codul „Divizia 15” și a fost subordonat directorului adjunct pentru magazine de aprovizionare și producția de carenă.
Succes la intersecția industriilor
Cooperarea metalurgiștilor și a constructorilor de tancuri a dus la crearea unui număr de tehnologii care, fără exagerări, pot fi numite adevărate descoperiri științifice și tehnice.
După ce au topit și laminat oțel blindat în foi, metalurgienii și-au transferat produsele către producția blindată a corpului. Aici metalul a fost tăiat conform șablonului în părțile corespunzătoare. În producția de „treizeci și patru”, în special multe probleme au fost provocate de două părți ale corpului: aripile (partea înclinată a lateralei) și placa laterală verticală. Ambele erau lungi, chiar și în benzi de lățime, cu tăieturi oblice de-a lungul marginilor.
Ideea sa sugerat în mod firesc să ruleze o bandă de măsurare egală în lățime cu părțile finite. A fost formulată pentru prima dată de mașinile blindate ale uzinei Mariupol în vara anului 1941. Pentru încercarea de rulare, am ales o moară de zăpadă la Zaporizhstal, unde au fost trimise două eșaloane de lingouri de armură. Dar apoi nu au avut timp să se apuce de treabă: trupele germane în avans au capturat atât eșaloanele, cât și Zaporozhye însuși.
La sfârșitul anilor 1941-1942, în timpul evacuării și dezvoltării producției de armuri la noile fabrici, nu exista o bandă suficientă. Cu toate acestea, în mai 1942, Comisariatul Popular al Metalurgiei Feroase a primit din nou un ordin de închiriere pentru tancurile T-34 și KV. Sarcina sa dovedit a fi dificilă: toleranțele în lățime nu trebuie să depășească -2 / + 5 milimetri, forma semilunii (îndoire) pentru lungimea totală a piesei a fost de 5 milimetri. Fisurile, apusurile și delaminarea nu erau permise la margini, astfel încât sudarea să poată fi efectuată fără prelucrare sau tăiere cu flacără.
Lucrările experimentale au început simultan în magazinele de rulare ale uzinelor metalurgice Magnitogorsk și Kuznetsk, la început fără realizări speciale. Închirierea de piese pentru tancurile KV a fost curând abandonată, dar T-34 a reușit în cele din urmă. Echipa de autori formată din șeful departamentului metalurgic al NII-48 G. A. Vinogradov, inginerul șef al KMK L. E. Vaisberg și inginerul aceleiași fabrici S. E. stă la „900” al morii feroviare și structurale este o complet nouă metoda de rulare „pe margine”. În ianuarie 1943, au fost emise 280 de benzi, în februarie - 486, în martie - 1636 bucăți. În aprilie, după toate testele necesare, a început dezvoltarea producției brute de benzi de măsurare pentru garniturile de arcuri ale roților tancurilor T-34. Inițial, au fost furnizate către UZTM și uzina de rezervoare Ural, apoi către alte fabrici - producători de tancuri T-34. Deșeurile, care inițial aveau 9,2 la sută, scăzuseră la 2,5 la sută până în octombrie 1943, iar benzile de calitate inferioară erau folosite pentru a realiza piese mai mici.
O evaluare completă și precisă a noii tehnologii este dată de raportul corespunzător al TsNII-48 din 25 decembrie 1943: „A fost dezvoltată, testată și introdusă în producția brută o metodă fundamental nouă de rulare a unei benzi largi blindate„ pe margine”., care a fost considerat irealizabil până de curând în URSS și în străinătate. Obținerea unei benzi calibrate (măsurate) cu lățimea părții finite a corpului blindat al rezervorului T-34 a făcut posibilă fabricilor NKTP să adopte o nouă tehnologie performantă pentru fabricarea pieselor blindate fără tăierea muchiilor longitudinale. Datorită aplicării noii metode la una dintre principalele părți blindate ale tancului T-34 (aripi), s-a realizat o economie de timp foarte semnificativă (aproximativ 36%) la tăierea acestora. S-au obținut economii de oțel blindat 8C până la 15% și economii de oxigen de 15.000 cbm la 1000 corpuri”.
Până la sfârșitul anului 1943, rularea unei benzi de măsurare a fost stăpânită pentru o altă parte a corpului T-34 - partea verticală a lateralei. Rămâne doar să adăugăm că autorii acestei invenții au primit Premiul Stalin pentru 1943.
În același 1943, prin eforturile comune ale laboratorului Institutului ucrainean al metalelor (condus de PA Aleksandrov) și al lucrătorilor din Combinația metalurgică Kuznetsk și a Uzinei de rezervoare Ural, a fost dezvoltat un profil laminat periodic periodic și stăpânit în producție pentru achiziții. a masei și a părților critice ale „treizeci și patru” - axe de echilibrare. Primul lot experimental al unui profil periodic a fost primit la KMK în decembrie, la începutul anului 1944, a început producția în serie. Până în octombrie, uzina de rezervoare Ural a trecut complet la fabricarea axelor de echilibrare dintr-un nou semifabricat, la sfârșitul anului, UZTM i s-a alăturat. Ca urmare, productivitatea ciocanelor de forjare a crescut cu 63 la sută și numărul de rupturi ale pieselor a scăzut.
Munca de succes a constructorilor de tancuri a fost mult facilitată de materialul rulant al fabricii de bandaj a uzinei metalurgice Novo-Tagil. Începând din primăvara anului 1942, au furnizat curele de umăr laminate cu cote reduse de prelucrare, în 1943 cotele au fost reduse din nou. În combinație cu noul instrument de tăiere, acest lucru a făcut posibilă efectuarea decupării consumatoare de timp a curelelor de umăr strict la timp și fără prea multă tensiune. Un caz rar: comisarul poporului pentru industria tancurilor V. A. Malyshev, în ordinul său din 28 septembrie 1943, a considerat necesar să exprime o recunoștință specială metalurgilor tagilieni.
Și, în sfârșit, ultimul exemplu: în 1943, jantele tancurilor de susținere T-34, mai întâi la uzina Chelyabinsk Kirov, apoi la alte întreprinderi, au început să fie realizate din produse laminate profilate speciale. Acest succes a fost remarcat și în ordinea lui V. A. Malyshev.
Rămâne să adăugăm că specialiștii companiei americane „Chrysler”, după ce au studiat tancul T-34-85 capturat în Coreea, au remarcat în special perfecțiunea golurilor de oțel din care a fost fabricat vehiculul de luptă. Și, de asemenea, faptul că au depășit adesea produsele întreprinderilor metalurgice americane.