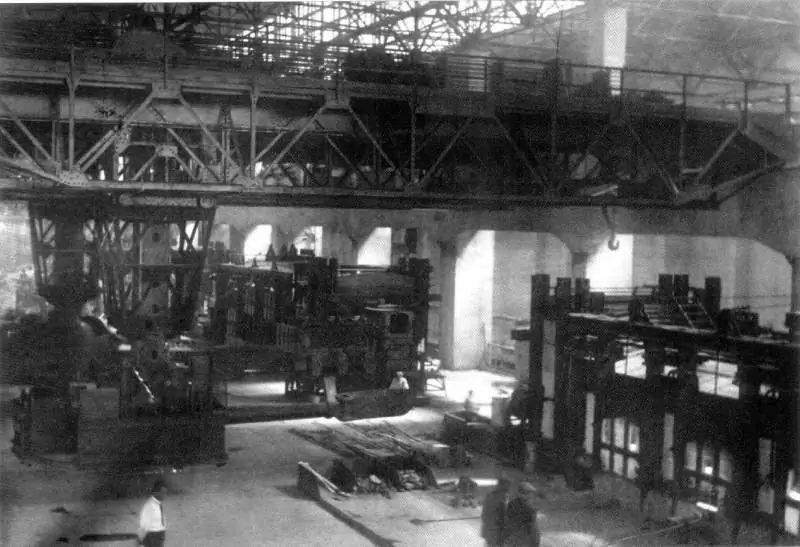
Resursă strategică
Este dificil să supraestimăm producția de oțel de înaltă calitate pentru complexul militar-industrial în condiții de război. Acesta este unul dintre cei mai importanți factori ai succesului armatelor pe câmpul de luptă.
După cum știți, metalurgii Krupp au fost printre primii care au învățat cum să producă oțel de înaltă calitate pentru arme.
Germanii au adoptat procesul de fabricație Thomas la sfârșitul secolului al XIX-lea. Această metodă de topire a oțelului a făcut posibilă îndepărtarea impurităților de fosfor din minereu, ceea ce a crescut automat calitatea produsului. Armurile și oțelurile de înaltă calitate din timpul primului război mondial au asigurat adesea superioritatea germanilor pe câmpul de luptă.
Pentru a organiza o astfel de producție, au fost necesare noi materiale refractare, care au căptușit suprafețele interioare ale cuptoarelor. Germanii au folosit ultimele refractare de magnezit pentru timpul lor, rezistând la temperaturi de peste 2000 de grade. Astfel de substanțe cu refractare mai mare se bazează pe oxizi de magneziu cu mici amestecuri de oxizi de aluminiu.
La începutul secolului al XX-lea, țările cu tehnologii pentru producția în masă de refractare de magnezit își permiteau să producă blindaje de înaltă calitate și butoaie de arme. Acest lucru poate fi comparat cu un avantaj strategic.
În ceea ce privește rezistența la foc, au fost mai scăzute așa-numitele materiale foarte refractare care rezistă la temperaturi cuprinse între 1750 și 1950 grade. Acestea sunt refractare dolomitice și cu conținut ridicat de alumină. Materialele refractare din argilă, semi-acid, cuarț și dină pot rezista la temperaturi cuprinse între 1610 și 1750 de grade.
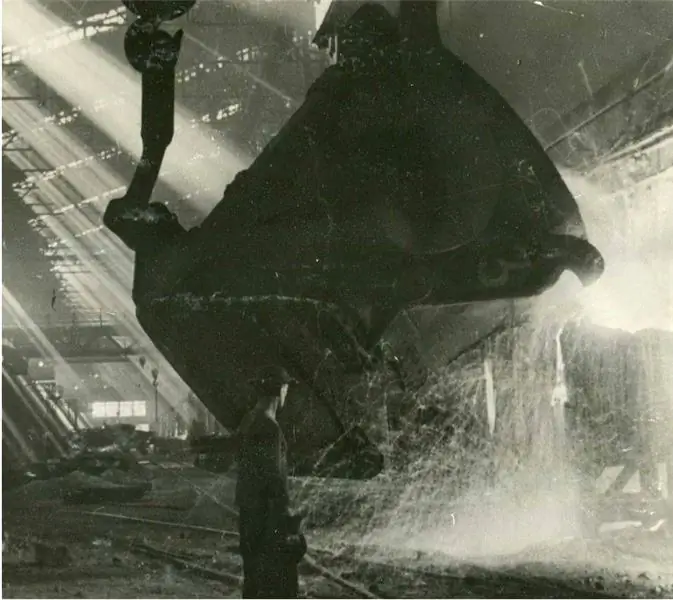
Apropo, tehnologiile și siturile pentru producerea de refractare de magnezit au apărut pentru prima dată în Rusia încă din 1900.
Cărămida refractară de magnezit Satka în 1905 a primit o medalie de aur la Expoziția Mondială Industrială de la Liege. A fost produs lângă Chelyabinsk, în orașul Satka, unde se afla un zăcământ unic de magnezită.
Mineralul periclază, din care se fabricau refractarele la fabrică, era de înaltă calitate și nu necesita îmbogățire suplimentară. Ca rezultat, magnezitul refractar de la Satka a fost superior omologilor săi din Grecia și Austria.
Reducerea decalajului
În ciuda cărămizii de magnezit de înaltă calitate de la Satka, până în anii 30, principalele refractare ale metalurgicilor sovietici erau materiale dinase din lut. Bineînțeles, obținerea unei temperaturi ridicate pentru topirea oțelului de arme nu a funcționat - căptușeala interiorului cuptoarelor cu focar deschis s-a destrămat și a necesitat reparații extraordinare.
Nu era suficientă cărămidă Satka și, în perioada postrevoluționară, principalele tehnologii de producție s-au pierdut.
În același timp, europenii au continuat - de exemplu, magnezita austriacă Radex s-a remarcat printr-o rezistență excelentă la foc.
Uniunea Sovietică a achiziționat acest material. Dar era imposibil să obții un analog fără un secret de producție. Această problemă a fost abordată de un absolvent al Universității Tehnice de Stat din Moscova. N. E. Bauman Alexey Petrovich Panarin. La fabrica Magnet (fostă combina Satka) în 1933 a condus laboratorul central al plantelor. Și cinci ani mai târziu, a lansat producția în masă de refractare periclază-cromită sau cromagnesită pentru cuptoare cu focar deschis.
La uzina metalurgică Zlatoust și la ciocanul și secera din Moscova, refractarul lui Panarin a înlocuit dinele învechite.
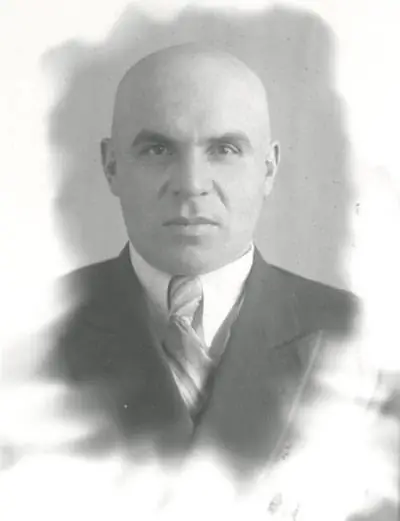
Tehnologia, care a fost dezvoltată în laboratorul „Magnezit” de câțiva ani, a constat într-o compoziție specială și dimensiunea particulelor.
Anterior, fabrica producea cărămizi convenționale crom-magnezit, formate din magnezit și minereu de fier de crom, într-un raport de 50/50. Secretul dezvăluit de grupul lui Panarin a fost după cum urmează:
„Dacă minereul de cromită din granulele granulometrice grosiere cu un conținut minim de fracțiuni mai mici de 0,5 mm se adaugă la o sarcină obișnuită de magnezită, atunci chiar și cu o adăugare de 10% a unui astfel de minereu, stabilitatea termică a cărămizii crește brusc.
Pe măsură ce adăugarea minereului de cromită de granulometrie grosieră crește, stabilitatea cărămizii crește și atinge un maxim la un anumit raport de componente."
Cromita pentru noul refractar a fost luată la mina Saranovskoye, iar periclaza a fost exploatată în continuare la Satka.
Pentru comparație, o cărămidă de magnezit „pre-revoluționară” obișnuită a rezistat la temperaturi de 5-6 ori mai mici decât noutatea lui Panarin.
La uzina de topire a cuprului Kirovograd, crom-magnezita refractară în acoperișul unui cuptor reverberator a rezistat la temperaturi de până la 1550 grade timp de 151 zile. Anterior, refractarele din astfel de cuptoare trebuiau schimbate la fiecare 20-30 de zile.
Până în 1941, producția de refractare pe scară largă a fost stăpânită, ceea ce a făcut posibilă utilizarea materialelor în cuptoare mari de oțel la temperaturi de până la 1800 de grade. O contribuție importantă la acest lucru a fost adusă de directorul tehnic al „Magnezit” Alexander Frenkel, care a dezvoltat o nouă metodă de fixare a materialului refractar la acoperișurile cuptoarelor.
Refractare pentru victorie
La sfârșitul anului 1941, metalurgii din Magnitka au realizat imposibilul anterior - pentru prima dată în istorie au stăpânit topirea oțelului blindat pentru tancurile T-34 din principalele cuptoare grele cu vatră deschisă.
Principalul furnizor de refractare pentru un proces atât de important a fost Satka "Magnezit". Nu este necesar să vorbim despre dificultățile din timpul războiului, când o treime din muncitorii fabricii au fost chemați pe front, iar statul a cerut ca planul să fie îndeplinit excesiv. Cu toate acestea, fabrica își făcea treaba, iar Panarin în 1943
"Pentru stăpânirea producției de produse foarte refractare din materii prime locale pentru metalurgia feroasă"
a fost distins cu Premiul Stalin.
În 1944, acest metalurgist-cercetător va dezvolta o tehnologie pentru producerea de pulbere de magnezită de înaltă calitate „Extra”. Acest semifabricat a fost utilizat pentru a prepara un refractar presat utilizat în producția deosebit de importantă de oțel blindat în cuptoare electrice. Limita de temperatură pentru astfel de refractare a atins 2000 de grade.
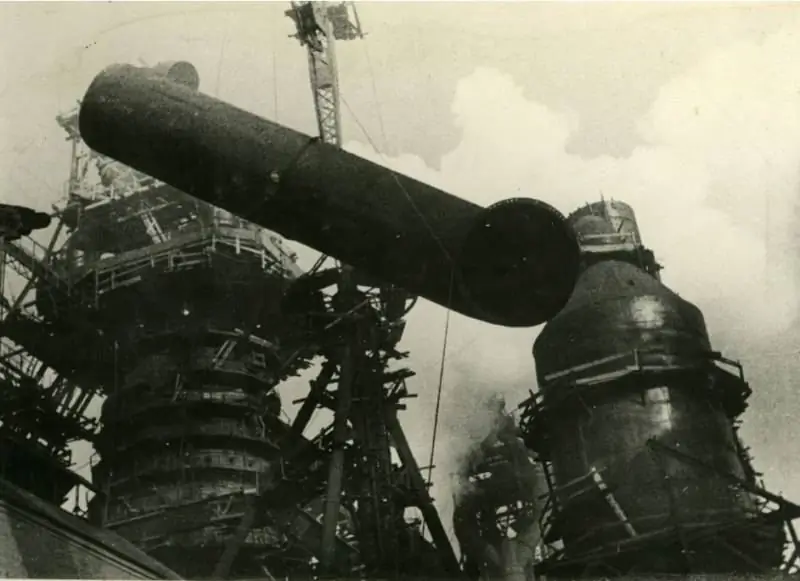
Dar nu ar trebui să presupunem că exemplul unei fabrici Magnezit de succes în general s-a extins la întreaga industrie refractară a Uniunii Sovietice.
O situație deosebit de dificilă s-a dezvoltat în Ural, unde practic toată clădirea tancurilor a fost evacuată în 1941-1942.
Uzinele metalurgice Magnitogorsk și Novotagilsk au fost reorientate către producția de armuri, furnizând produse către Sverdlovsk Uralmash, Chelyabinsk „Tankograd” și uzina de rezervoare Nijni Tagil nr..
De exemplu, în Magnitka, fabrica dinas-șamotă a produs 65-70 mii tone de cărămizi pe an. Acest lucru nu a fost suficient nici măcar pentru propriile nevoi, ca să nu mai vorbim de aprovizionarea către alte întreprinderi.
Primele dificultăți au apărut atunci când fabricile de tancuri au început să-și construiască propriile cuptoare de încălzire și termice. Metalurgia urală abia avea deja suficiente materiale refractare, iar apoi producția corpului de cisterne a necesitat materiale de înaltă calitate pentru căptușirea cuptoarelor.
Aici nu s-a vorbit despre niciun refractar de cromagnesită aici - acest material a fost în cantitate redusă și chiar a fost exportat în schimbul unui împrumut-împrumut american. Cel puțin acest lucru este menționat într-o serie de surse. Istoricii Uralului scriu că scumpul cromagnezit al lui Panarin ar putea merge în străinătate în schimbul unor feroaliaje rare pentru armura tancurilor. Dar nu există încă dovezi directe în acest sens.
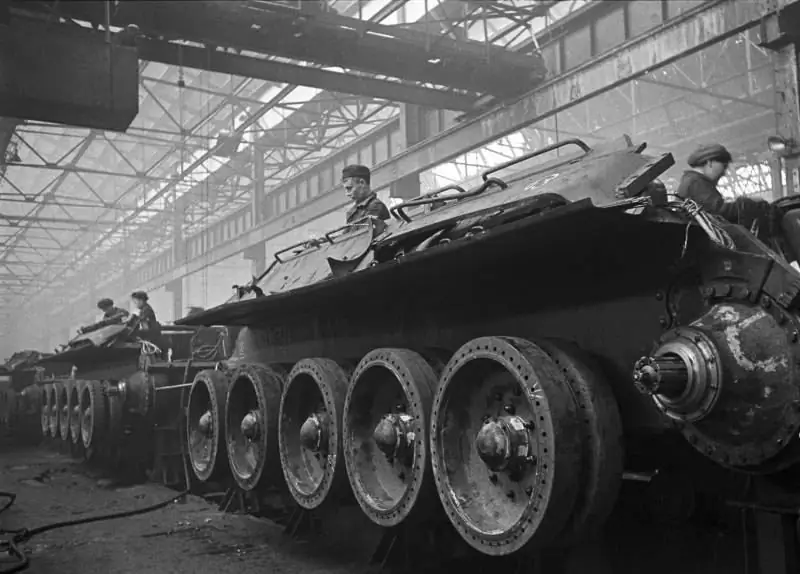
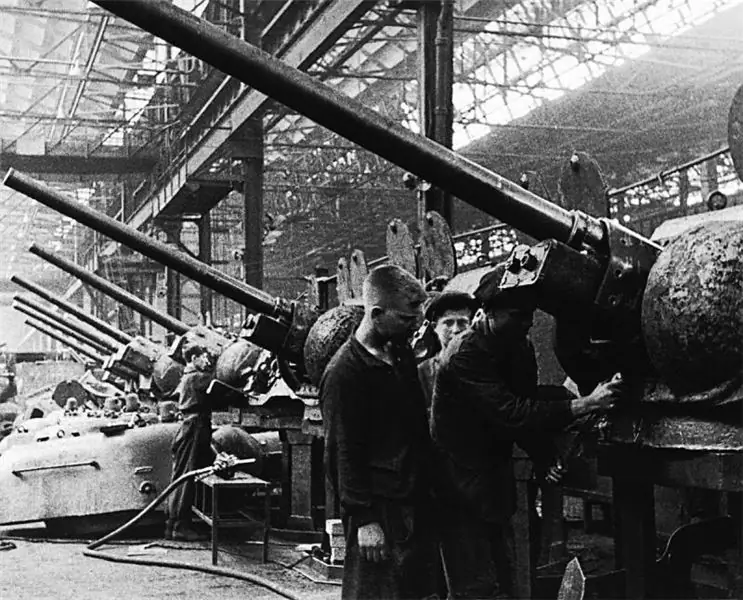
Fabricile de tancuri se bazau în cea mai mare parte pe material refractar dinas produs de fabrica Pervouralsk. Dar, în primul rând, a fost produs doar 12 mii de tone pe lună și, în al doilea rând, metalurgii au preluat partea de leu.
Extinderea producției la uzina din Pervouralsk a mers foarte încet. Și la mijlocul anului 1942, au apărut doar 4 cuptoare noi. Restul fie nu erau gata, fie existau în general doar în proiecte.
Refractarele pentru cuptoarele cu vatră deschisă ale fabricilor de tancuri au venit adesea de proastă calitate, nu în totalitate și la momentul nepotrivit. Doar pentru repararea cuptoarelor Uralmash în al patrulea trimestru al anului 1942, au fost necesare 1035 tone de cărămizi rezistente la foc și s-au primit doar aproximativ 827 tone.
În 1943, atelierul deschis din Uralmash, în general, aproape a încetat din cauza lipsei refractarilor pentru reparații.
Calitatea refractarilor furnizate pe tot parcursul războiului a lăsat mult de dorit. Dacă în condiții normale, cărămida dină a cuptorului cu focar deschis ar putea rezista la 400 de călduri, atunci în război nu a depășit 135 de călduri. Și până în martie 1943, acest parametru scăzuse la 30-40 de călduri.
Această situație demonstrează în mod clar cum lipsa unei resurse (în acest caz, refractare) poate încetini serios activitatea întregii industrii de apărare. După cum scrie candidatul la științe istorice Nikita Melnikov în lucrările sale, în martie 1943, trei cuptoare cu focar deschis ale Uralmash s-au oprit și au efectuat un ciclu complet de lucrări de reparații. A fost nevoie de 2346 de tone de dina, 580 de tone de șamotă și 86 de tone de magnezită redusă.
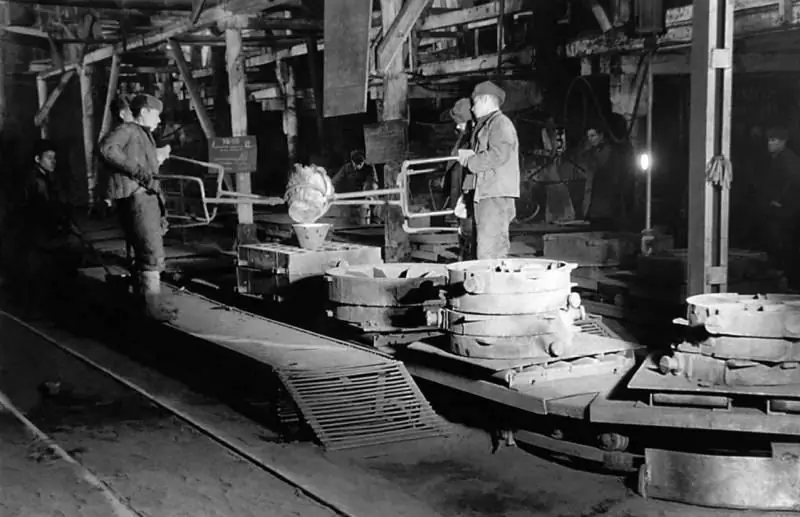
Până la mijlocul anului 1942, la uzina de tancuri nr. 183, situația se dezvolta în mod similar - producția de oțel a rămas în urma asamblării mecanice. Și a trebuit să „importăm” corpurile T-34 de la Uralmash.
Unul dintre motive a fost lipsa de refractare pentru repararea cuptoarelor cu focar deschis, care în primăvara anului 1942 lucrau la limita lor. Drept urmare, doar 2 din 6 cuptoare cu focar deschis erau în funcțiune în toamnă, iar volumele de topire au fost restaurate abia în a doua jumătate a anului 1943.
Situația cu refractare în structura complexului de apărare sovietic din timpul Marelui Război Patriotic ilustrează clar complexitatea situației din spatele țării.
O penurie cronică de, în general, nu cel mai înalt produs tehnologic a afectat direct ritmul de producție al vehiculelor blindate.